シュナイダーエレクトリック でのフランジ部品の ケース
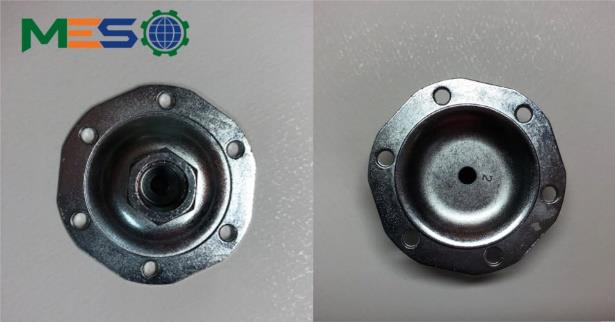
米国で照明器具を生産するシュナイダーエレクトリックは、グローバルに使われている部品であるフランジについて、その高いコストと部品の安定供給について問題を抱えていました。MESに対し課せられた課題は、その部品のグローバルな供給を保証し、コストを下げることでした。MESはこのシュナイダーエレクトリックからの要求に対して、よく考慮された解決法で迅速に対応することができました。
「問題点」
部品は、ステンレススチールのナットとフランジからできていました。この二つの部品は比較的高価でしたが、屋外で使われることを考慮して、湿度が高くまた低温下での使用、さらに腐食環境で使用されても、製品の腐食および機能障害が起きないことを考慮してステンレススチールの素材が選ばれました。
ナットはフランジにロウ付けされていました。素材としてのステンレススチールの使用、およびロウ付けの工程は製造コストの上昇をもたらし、シュナイダーエレクトリックは、最終製品の耐久性を維持したまま、コストを下げる方法を探していました。
「MESの解決法」
MESは、部品の耐腐食性を維持したまま、部品の生産コストをさげる解決策を提案しました。MESが提案したのは、ステンレススチールのナットとフランジの部品を、亜鉛のダイカストの一体品で置き換えることでした。
この変更により生産工程でのロウ付け作業が省かれ、コストが低減されました。さらに、MESは亜鉛ダイカスト部品に特別な表面処理をほどこし、ステンレススチールと同じレベルの耐食性および耐久性を達成しました。
「MESが導いた結果」
MESは、ステンレススチール部品から亜鉛ダイカストの一体部品までの変更を、設計、試作、性能および耐久試験を含め、全面的な新製品の生産開始までをたったの12か月で行いました。
亜鉛ダイカスト部品は中国の生産委託先で作られましたが、その生産管理、品質管理、物流管理はMESの100%子会社である中国の寧波メトリックスが行いました。
MESの営業部長のマイクデントは「ナットとフランジの組み立て部品から、亜鉛ダイカストの一体部品に変えることで、シュナイダーエレクトリックは部品の生産コストをグローバルな規模で低減することができた」と語っています。
さらに、「コスト低減を持続していくことは、今日のビジネスにおいて重要であり、今回のシュナイダーエレクトリックでのケースによって、コスト低減を行うには、製品設計、生産、物流管理まで含めた、総合的で多方面にわたる考察が必要であることが再認識された。これがTotal Engineering Solutionである」と付け加えました。
メトリックスジャパンを含むMESグループは皆様が数多くお持ちの製品開発における問題点を製品設計、生産、物流管理まで含めた、総合的な判断で迅速に問題解決のノウハウをグローバルな視点で有するTotal Engineering Solutionを基本コンセプトに活動する企業集団です。
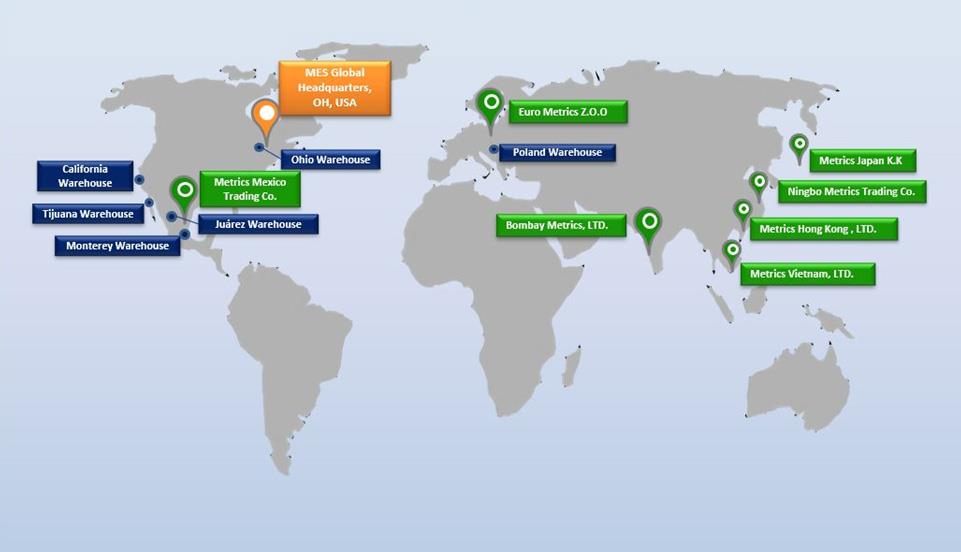